In the realm of manufacturing premium furniture, effective communication stands as the doundation of success. Balagi, a renowned furniture manufacturer, attributes its excellence to its unwavering commitment to communication.
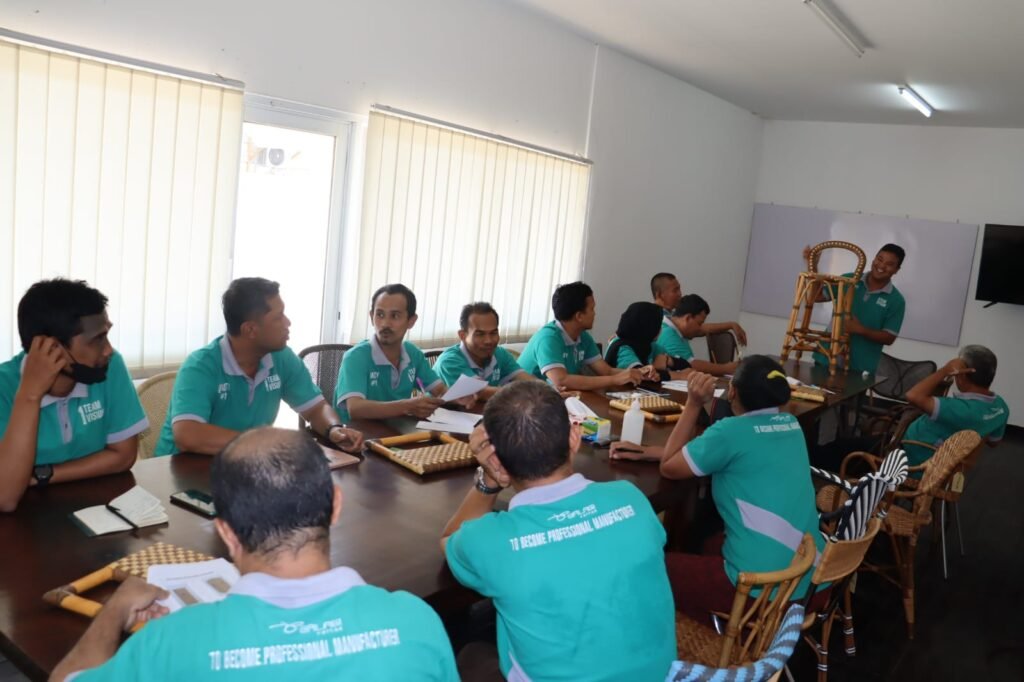
The point of this commitment is the Pre-Production Meeting (PPM), a forum where all relevant departments converge to elucidate the techniques and processes involved in crafting each item. Spearheaded by the Research and Development (R&D) Department, the PPM serves as a platform for collaboration, ensuring that every facet of production is meticulously planned and executed.
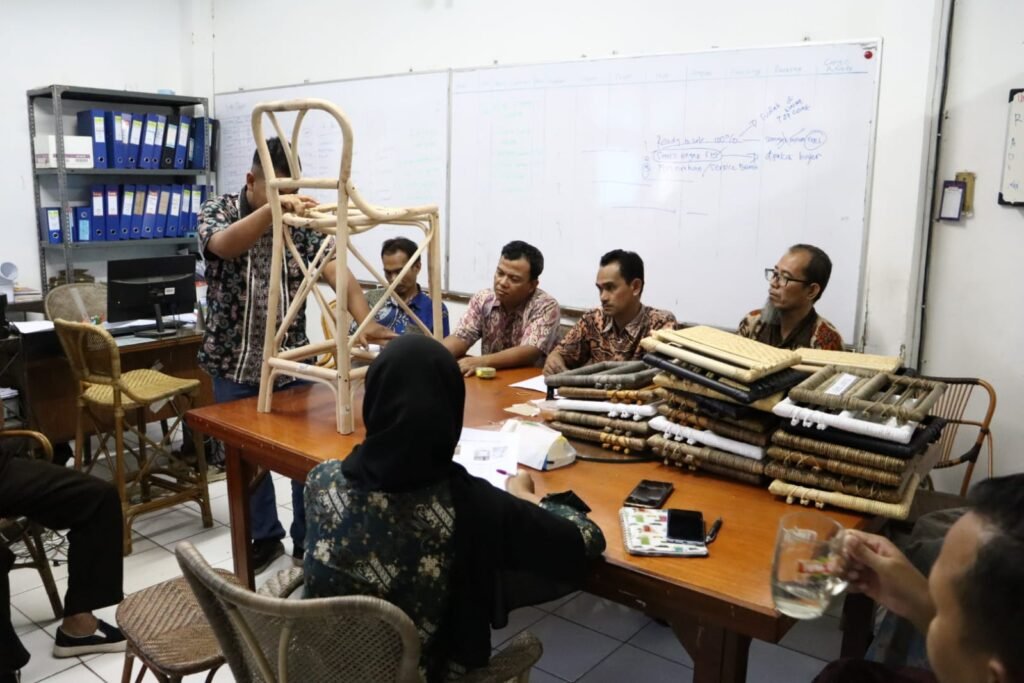
The Pre-Production Meeting (PPM) serves as an important point in the production of Balagi. The primary objective of the PPM is to share the important information regarding the production techniques and requirements for the items
The PPM is a multi-disciplinary affair, drawing participation from key departments such as Marketing & Sales, Export, Quality Assurance & Quality Control (QA & QC), and Production. Each department brings unique insights and expertise, enriching discussions and driving approaches to production management.
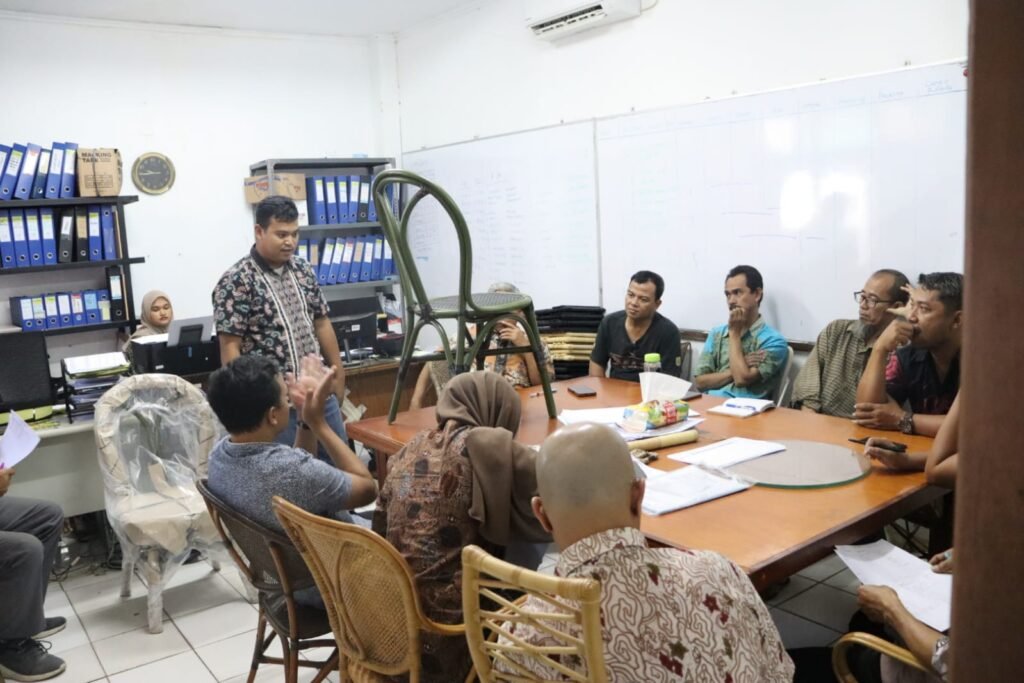
Point success of the PPM is the meticulous preparation undertaken by the R&D Department. Prior to the meeting, R&D ensures that all the requires data pertaining to the item is ready and available.
One crucial component of this preparatory phase is the Master Copy Sample (MCS). The MCS serves as a benchmark for production, providing a tangible reference point for the manufacturing team. By equipping the Production Department with the MCS, R&D empowers them to adhere to established standards and specifications throughout the production process.
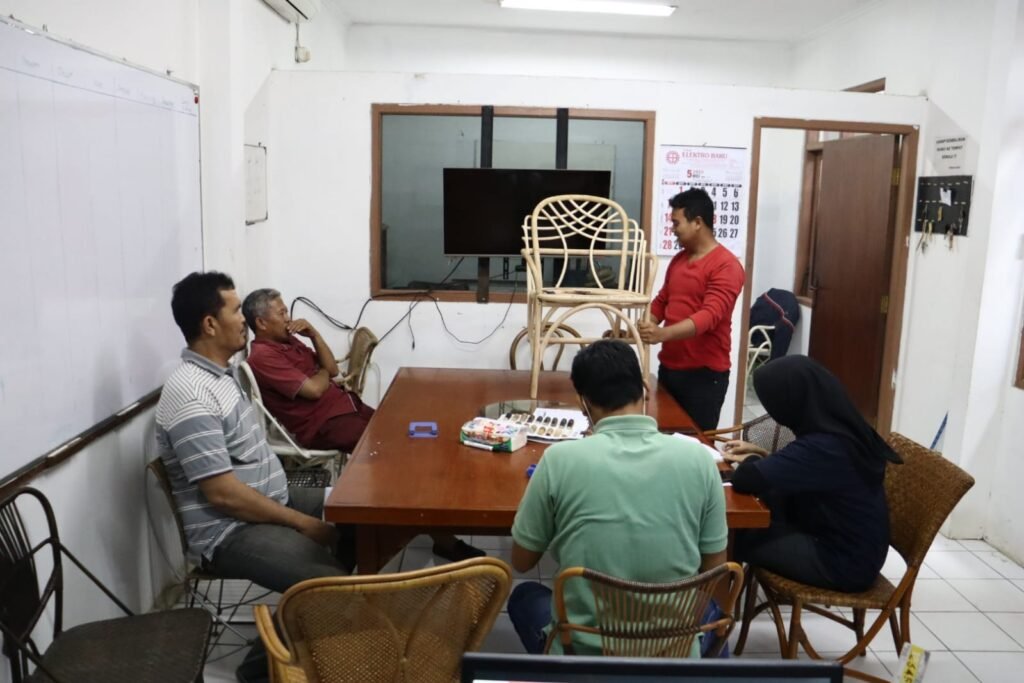
By maximizing the collective expertise of all involved departments and obey the standard of preparation, Balagi continues to set production benchmarks to produce high-quality furniture.